The people, materials, finance, and sales are the basis of enterprise management. It is from the point of view of business management. A successful enterprise, its warehouse management is certainly good. Suppose you are forming a warehouse or preparing to update your warehouse. You need to understand the importance of warehouse organization.
What is Warehouse Organization?
Warehouse organization is primarily a method of storing inventory using vertical storage. It is like placing items on pallet racks. It allows you to maximize your warehouse space more than horizontal storage. Let’s say you have a small warehouse and need to store many goods soon but can’t buy more space. Then storing your inventory vertically is the best way to go and is very cost-effective.
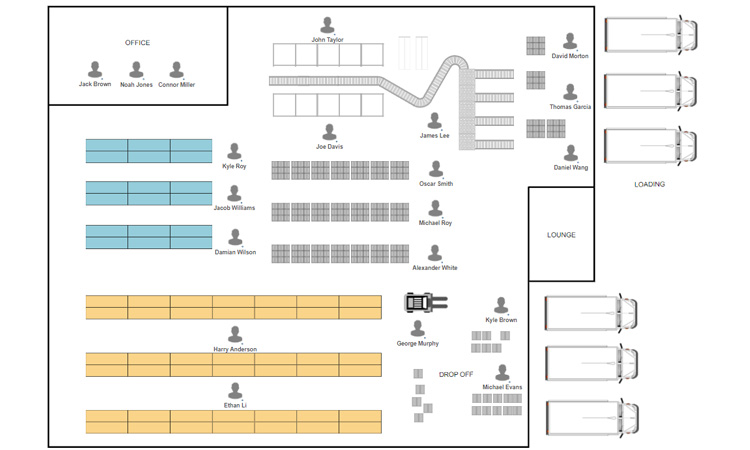
So How do You Organize Your Warehouse?
Suppose a business wants to maintain adequate facilities continuously. It needs to manage its warehouse inventory effectively. The smoothness of a company’s warehouse operations can also be seen in managers’ measures to organize their inventory. Even if you think everything is fine, you must improve it frequently. You can consider whether your warehouse is deficient by following these implementations. It will allow you to make full use of your limited space.
It may be helpful for you to consider and implement these measures for organizing your warehouse.
- You must locate best-selling products at the front of the warehouse
- Same selling products close to each other
- Information labels and product photos are used together
- Warehouse aisles are neatly arranged
- Warehouse items are placed in stacks to make good use of vertical space
- You can place Smaller items in stacking bins
- Seasonal products can be placed in mobile shelving units
- Sufficient space in the receiving area
- Continually looking for ways to improve the organization of the warehouse
These measures help managers to organize warehouse inventory better. It also helps to improve the efficiency of inventory management.
How can You Organize the Layout of Your Warehouse?
Warehouses can be seen as the foundation of your business. The organization is key to maintaining the success of your business. Suppose you operate a disorganized warehouse that needs to be improved for new opportunities. Your first consideration may be to organize the layout of your warehouse. Here are some processes you can optimize to help your employees complete their daily tasks more efficiently
Warehouse Organization Plan
It is best if your warehouse is in the preparation-design phase. You can set it up from scratch, eliminating most of the hassle. Of course, the warehouse you are running can also be rearranged, although this can be a long process.
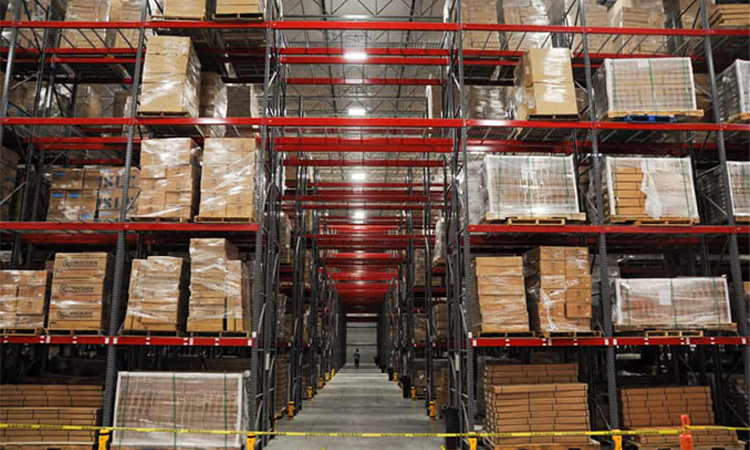
Employees are in a safe and productive workspace that helps them be more productive. You might consider setting up your workflow in order of operation. Depending on the storage method, place incoming inventory into one or more storage areas. When a new order is received, the assigned area is packaged and transferred directly to the logistics chain for distribution. Inventory lines need to be kept clear during the implementation process. That is, there is a relatively straight line from where you enter your facility to how you handle it to how you leave.
Frequent communication with employees helps get more constructive ideas for improvement. Listening to them and keeping employees safe and happy benefits everyone.
Keeping Your Warehouse Tidy
Companies can use labels and tags to mark the entire warehouse inventory and work areas. Marking them helps businesses maintain organization and facility processes over the long term. Once your warehouse layout is established, you may consider using labels. Labels allow employees to know more quickly where their items or locations are. It is especially beneficial for new employees or temporary workers.

Don’t limit your focus to inventory and work areas. You may also want to consider adding signage to dangerous areas of the warehouse. It will ensure the safety of your employees. It can reduce errors or misplacement of other valuable inventory.
Companies can prepare many maps of inventory locations to help employees navigate the warehouse. For older workers, labels and signage communicate what they need to know. They don’t need a map. But for new employees or temporary workers, a map can be a very helpful thing. People know exactly where they are going and can get work done relatively faster.
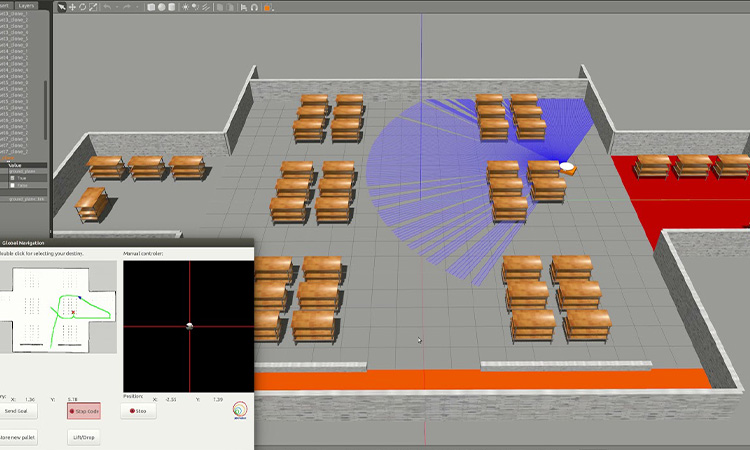
Check the Maximum Value the Warehouse can Hold
A warehouse is like another home for you. Now that we have marked everything in the warehouse, it’s time to check the maximum amount that the warehouse can hold. You can use the simplest mathematical formula to calculate it.
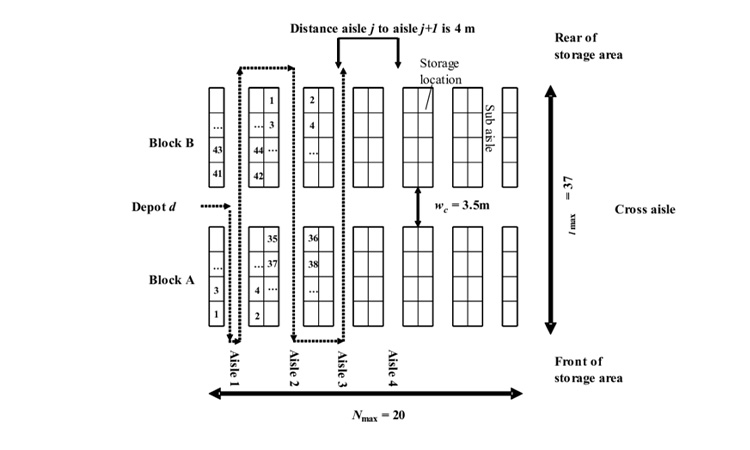
Height x Width x Depth = Storage Capacity (Cubic Feet)
Assuming you use traditional shelving and racking in your warehouse, you have a few more questions to consider.
- What is the spacing of the shelves?
- Is there wasted space on top of the product on the shelves?
There is no need to waste this space. The space is additional spaces that you can use in addition. Companies must consider arranging to eliminate any “air space.” It is best to arrange the storage space as compact as possible and make the products easy to use.
You can maximize space utilization by investing in automated storage and retrieval devices. They can provide a higher storage density in a more compact space than manual devices. They also generally have a return on investment of fewer than 18 months. Three types are typically available.
- Horizontal Carousel Module (HCM) – It consists of several boxes. These boxes are mechanically connected to an overhead or floor-mounted drive track to form a complete loop. Storage locations are rotated on an oval track and delivered to employees at picking locations. It greatly reduces non-productive travel and searches time for employees.
- Vertical Carousel Module (VCM) – It resembles a Ferris wheel-like layout and consists of a series of shelves that rotate around a track. It ensures the safety of stored items under the command of the staff. It also quickly transports items to ergonomic workstations. It eliminates employee walking as well as item search time.
- Vertical Lifting Module (VLM) – It is an enclosed automated storage and retrieval system. It consists of two rows of trays and inserters/retrievers. When running, the middle inserter/extractor locates the desired tray from the two columns. It will present the specified pallet to the operator in a waist-high pickup window. It eliminates operator travel and SKU search time.
Each of these types of systems has its distinct advantages over traditional shelving. They all reduce the amount of space and floor space required without the need for additional expansion. They can store more products in the same facility footprint to achieve maximum space utilization. The company can leverage them further by increasing the number of SKUs stored.
How to Manage Your Warehouse Effectively?
We have planned the general layout of the warehouse in the previous section, and the next is the most important inventory management. Inventory management refers to tracking and managing all the physical objects in the warehouse. For employees, the warehouse is a large and very large number of items. Getting their work done without a system to track these physical assets is difficult. Companies need to categorize their inventory as well as use proper storage methods. It allows you to maximize the use of your existing facilities. It also helps you to free up previously wasted space and increase capacity. It also helps employees to be more productive.
Inventory Sorting
Inventory sorting ensures that you organize your inventory accordingly. It would help if you had the appropriate data to analyze your inventory units or SKUs. You can take an inventory based on the items in the warehouse, the frequency of movement, or the frequency of picking. Among the items to be considered, options should consider their size, shape, and quantity. You can classify the inventory into A, B, C, and D categories. Where A is a fast mover, B is a medium mover, C is a slow mover, and D is a very slow mover. Once they are divided, they can be represented in a chart. Subsequently, cross-reference the recorded SKU speed with the time required for the item. It will tell you how much it costs to pick your inventory.
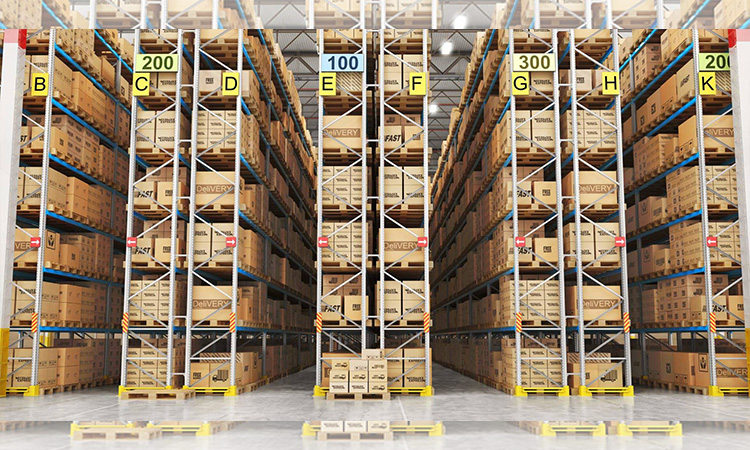
Using the Pareto principle here (80/20 rule) is very wasteful. Because it doesn’t make sense for you to spend 80% of your time on only 20% of your inventory. You can easily miss improvement opportunities for the remaining 80% of your inventory. Then those remaining inventories will stagnate.
Clear Out Inventory
Certain products on the shelves in the warehouse never seem to diminish. Unlike popular items, slow-moving products are hard to sell. Most businesses will always have them in their warehouses. They are taking up the limited space in your warehouse. You need to be aware of the products in your warehouse to eliminate the ones that are hard to sell. You can eliminate them by reducing their inventory or finding other ways.
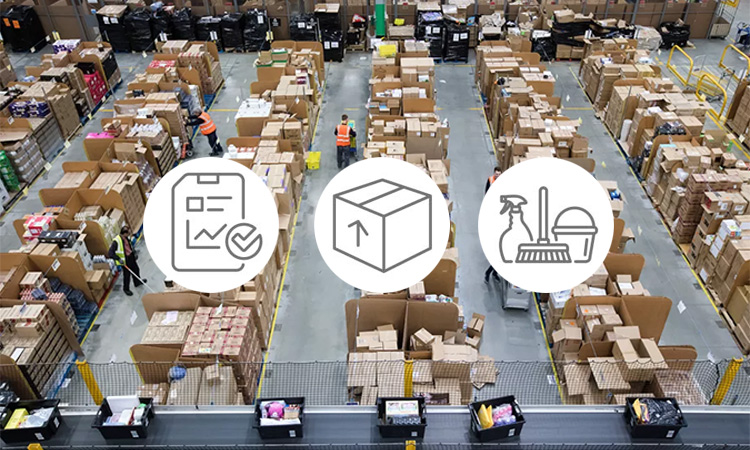
Warehouse Management System
It is not difficult for enterprises to see that managing a warehouse is extremely complicated. It can be a headache, especially for businesses with large physical assets. The emergence of warehouse management systems has given companies solutions. Many warehouse management systems are on the market, such as RFID, barcode management systems. They all help you to have a better understanding of your warehouse inventory.
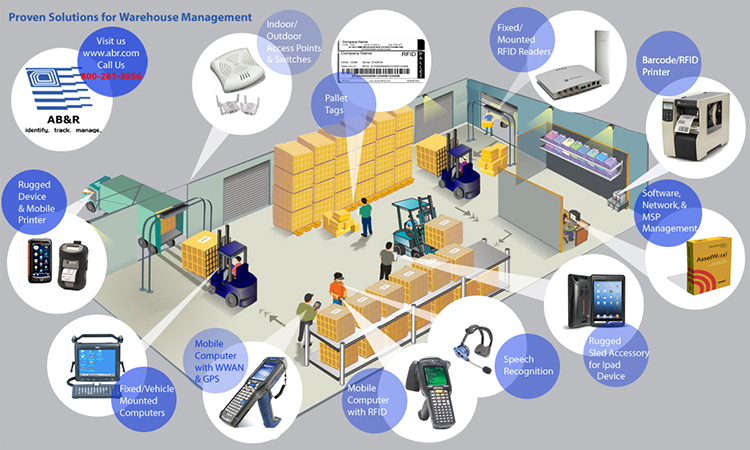
It can also help your employees to find the required items more easily. It can even help businesses speed up the shipping process.
Picking the right warehouse management system can help you better control your inventory. When you use them, you will see that managing your warehouse is not that difficult.
Inventory is a necessity to maintain business activities. The warehouse with inventory plays a very important role in the production and distribution of goods. Finding the right warehouse organization is a very important thing in this regard. It allows the company to achieve maximum utilization of the limited space. At the same time, it is also important to take appropriate warehouse management measures. It can improve the competitiveness of enterprises.
About Warehouse Organization Problem
-
How can businesses use data and analytics to optimize warehouse organization and improve performance?
Data and analytics can be used to identify trends, optimize inventory levels, and improve operational efficiency. Data visualization software and predictive analytics can help businesses make data-driven decisions.
-
What are some best warehouse inventory management practices, and how can they be implemented?
Best practices for inventory management include cycle counting, ABC analysis, and safety stock management. They can be implemented through inventory management software and process improvement initiatives.
-
How can warehouse layout and design impact organization and efficiency, and what factors should be considered?
Warehouse layout and design can impact organization and efficiency by affecting product flow, accessibility, and safety. Factors such as space utilization, product characteristics, and order fulfillment requirements should be considered when designing a warehouse layout.
-
How can businesses measure the success of their warehouse organization efforts, and what metrics should be used?
Metrics such as inventory accuracy, order fulfillment rates, and cycle time can be used to measure the success of warehouse organization efforts. Regular performance reviews and benchmarking against industry standards can also provide insights into areas for improvement.
-
How can businesses ensure compliance with regulations and standards related to warehouse organization, such as OSHA regulations and ISO standards?
Businesses can ensure compliance by staying up-to-date with the latest regulations and standards, providing employee training on safety and compliance, conducting regular safety audits, and investing in equipment and infrastructure that meet regulatory requirements.
-
What are some strategies for optimizing space utilization in the warehouse, and how can businesses implement them?
Optimizing space utilization includes using vertical space, implementing standardized storage systems, employing cross-docking and just-in-time inventory techniques, and investing in automation technology. Businesses can implement these strategies by analyzing their space utilization needs, investing in the necessary equipment and infrastructure, and training employees on best practices.
-
How can businesses ensure effective communication and collaboration among different teams and departments involved in warehouse organization, such as logistics, operations, and IT?
Businesses can ensure effective communication and collaboration by establishing clear lines of communication, using collaboration tools such as project management software and video conferencing, fostering a culture of teamwork and collaboration, and providing training on effective communication and collaboration. Regular meetings and cross-functional team-building activities can also help improve communication and collaboration.