The gas sensor is one of the important devices for people to detect the composition and concentration of gas. It provides enough security for people’s safe production. In this paper, we will discuss six main types of gas sensors. These include semiconductors, thermal conductivity, solid electrolytes, and electrochemical gas sensors. And some catalytic combustion and optical types of gas sensors.
What are Gas Sensors?
The gas sensor can detect the presence or absence of a target gas in a specific area. People also use it to measure the concentration of a target gas component. It uses a method to convert the volume fraction of the target gas into an electrical signal.
The gas sensor calculates the concentration of the target gas component in a certain area based on physical and chemical action. Then it converts the obtained information into a standard electrical signal. The user can track and analyze a specific gas based on the collected information.
The detection head of the gas sensor will have a conditioning effect on the gas sample. The detector head will filter out impurities and interfering gases and dry or refrigerate to handle the display part of the meter.
In real life, people mostly apply it to detect toxic and hazardous gases and natural gas leaks.
List of different types of gas sensors and the gases they detect:
Gas Sensor Type | Gases Detected |
---|---|
Carbon Monoxide (CO) Sensor | Carbon Monoxide |
Methane (CH4) Sensor | Methane |
Hydrogen Sulfide (H2S) Sensor | Hydrogen Sulfide |
Oxygen (O2) Sensor | Oxygen |
Volatile Organic Compounds (VOC) Sensor | Benzene, Toluene, Xylene, and other VOCs |
Nitrogen Dioxide (NO2) Sensor | Nitrogen Dioxide |
Ammonia (NH3) Sensor | Ammonia |
Carbon Dioxide (CO2) Sensor | Carbon Dioxide |
Chlorine (Cl2) Sensor | Chlorine |
Sulfur Dioxide (SO2) Sensor | Sulfur Dioxide |
Types of Gas Sensors
Many types of gas sensor technology exist on the market. We can classify them into four main categories depending on how the reaction occurs. These categories are electrochemical, infrared, contact combustion, and semiconductor gas sensors. The reaction mechanism can be classified as electrochemical, electrical resistance, ultrasonic, etc.
Based on the sensor detection principle, some of our common types of gas sensors are:
- Semiconductor-type Gas Sensors
- Thermal Conductivity Gas Sensors
- Solid electrolyte Gas Sensors
- Electrochemical Gas Sensors
- Catalytic Combustion Gas Sensors
- Optical Gas Sensors
Semiconductor Gas Sensors
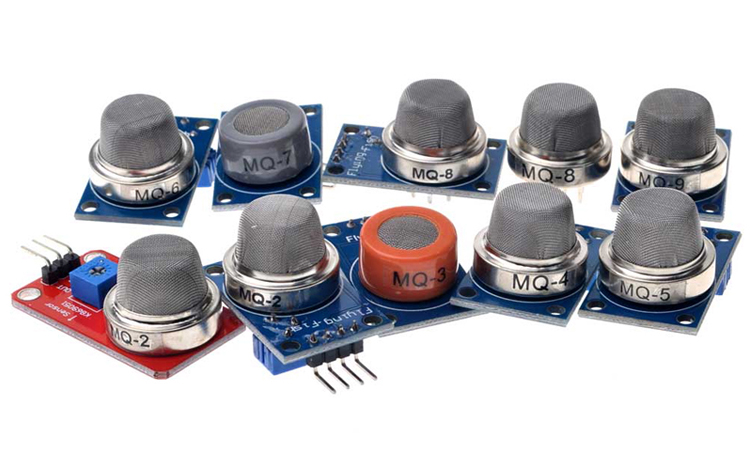
Semiconductor gas sensors meet the detection needs of various civil gases. This sensor accounts for almost 60% of gas sensors. Semiconductor gas sensors can be divided into two types depending on the materials used. One is the common metal oxide semiconductor gas sensor. And the other one is an organic semiconductor gas sensor. Both can easily get information about the material used from the name. The conductivity of this type of sensor varies with the content in the ambient target gas at a specific temperature. A more typical example is the alcohol sensor. Tin dioxide decreases in resistance when it encounters the alcohol gas in the alcohol sensor.
Advantages:
- Simple structure.
- Low price.
- High detection sensitivity.
Disadvantages:
- Small measurement linear range.
- Susceptible to background gas interference.
- Susceptible to ambient temperature.
Thermally Conductive Gas Sensors
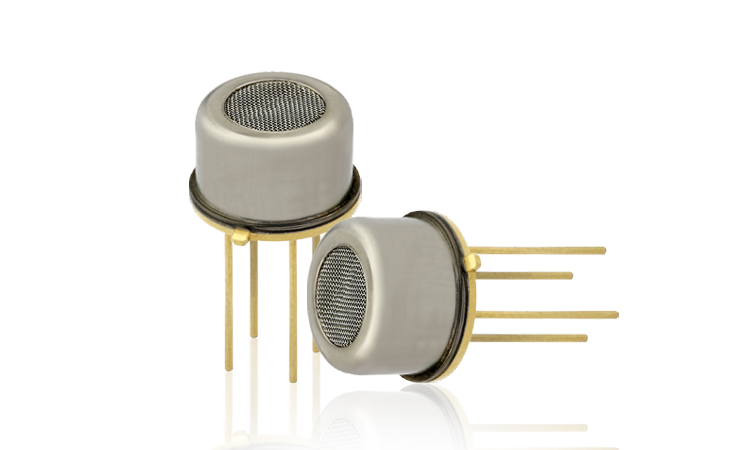
Thermal conductivity gas sensors were the first sensors used by man for gas detection. This sensor converts information related to the gas into an electrical signal. The information it collects helps researchers to detect and analyze the target gas. The working principle of thermal conductivity gas sensors is simple. They are based on the fact that the thermal conductivity changes with the content of the target gas. Each gas has its specific thermal conductivity. One can distinguish these gases with widely varying thermal conductivities using conductive elements. Such sensors are widely used to detect hydrogen, carbon dioxide, and methane.
Thermal conductivity of different gases:
Gas | Temperature ℃ | Thermal Conductivity W/(m·℃) |
Hydrogen | 0 | 0.17 |
Carbon Dioxide | 0 | 0.015 |
Air | 0 | 0.024 |
Air | 100 | 0.031 |
Methane | 0 | 0.029 |
Water Vapor | 100 | 0.025 |
Nitrogen | 0 | 0.024 |
Ethylene | 0 | 0.017 |
Oxygen | 0 | 0.024 |
Ethane | 0 | 0.018 |
Advantages:
- Good stability.
- Long service life.
- Accurate measurement.
Disadvantages:
- Narrow application range.
- Many limitations.
Read more: How to Test 3 Wire Crank Sensor with Multimeter
Solid Electrolyte Gas Sensors
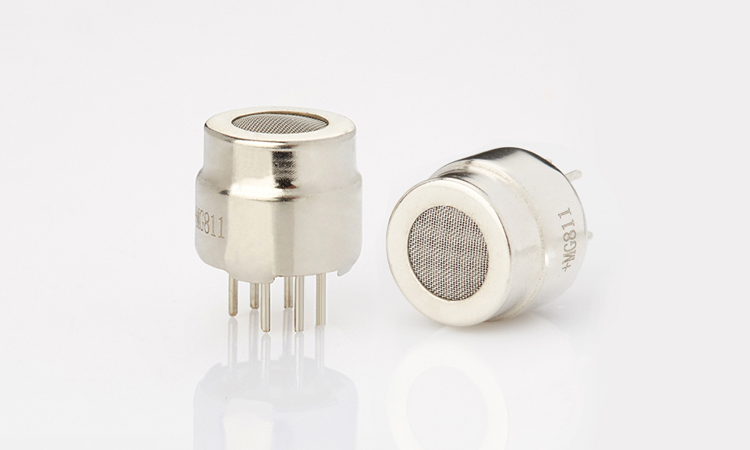
The solid electrolyte gas sensor is a highly selective gas detection sensor. The sensor relies on the migration of ions or protons. They also rely on the potential difference created by the conduction of ions or protons to determine the gas concentration. The ZrO2 oxygen sensor is one of the most representative gas detection sensors. This sensor has a fast response and can be tracked for continuous detection. Solid electrolyte gas sensors are used in metallurgy, petrochemical, aerospace, and transportation.
Advantages:
- High sensitivity.
- Long service life.
- High conductivity.
Disadvantages:
Long response time.
Electrochemical Gas Sensors
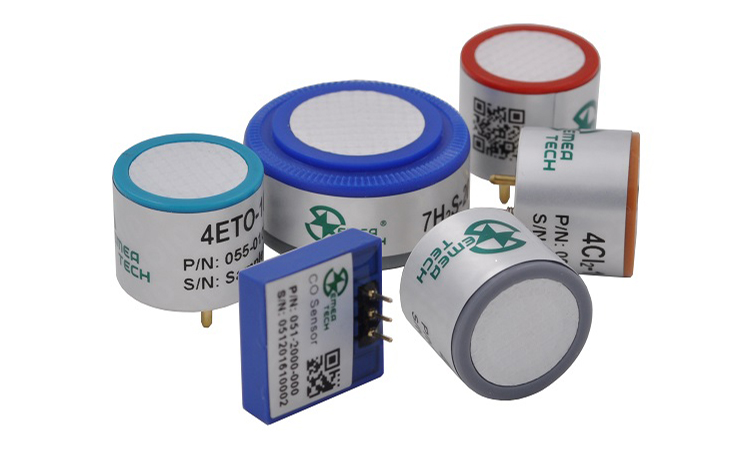
Electrochemical gas sensors mainly use the electrochemical activity of the gas being detected. They electrochemically oxidize or reduce the target gas. They will use these chemical reactions to distinguish the composition of the gas from it and detect its concentration. Electrochemical gas sensors are mostly used to measure the concentration of a specific gas in an external circuit.
The following two gas sensors are commonly used in an electrochemical way:
Primary cell-type gas sensors operate on a similar principle to dry cells. They differ in that a gas electrode replaces the carbon-manganese electrode of the cell. There are many gases that this sensor can detect. Among them are oxygen, sulfur dioxide, and chlorine gas. Take the example of detecting oxygen concentration. Oxygen is reduced as it enters the cathode. The reduced electrons flow through the ammeter to the anode. At the same time, the lead metal there is oxidized. In this process, the current size is correlated with the oxygen concentration. The sensor has a very high sensitivity.
The constant potential electrolytic sensor will place the gas to be detected in a specific electric field. And then it will ionize these gases. At the same time, they will detect the gas concentration by the electrolytic current flowing through it. This type of sensor is particularly suitable for the detection of reducing gases. The sensors are important for the detection of toxic and hazardous gases. They are widely used for gas monitoring carbon monoxide, hydrogen sulfide, ammonia, etc.
Advantages:
- Small size.
- Low power consumption.
- Long life.
- Resolution up to 0.1 ppm.
Disadvantages:
- Susceptible to interference.
- Sensitivity is easily affected by temperature differences.
Read more: How to Test ABS Sensor
Catalytic Combustion Gas Sensors
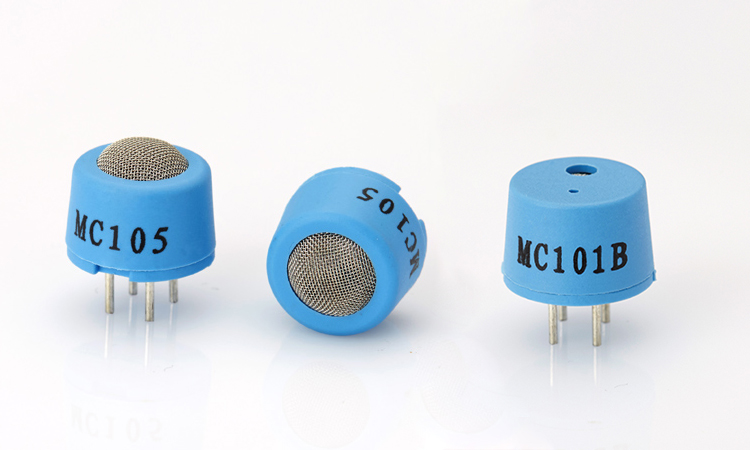
Catalytic combustion gas sensors are suitable for detecting explosive hazard combustible gases. These flammable gas concentrations are between the lower explosive limit (LEL) and the upper explosive limit (UEL). These sensors have a high temperature-resistant catalyst layer on the surface of the platinum resistor. The combustible gas is catalytically burned on its surface when the temperature threshold is reached. During this process, the combustion affects the platinum resistor and the temperature increases. At the same time, the resistance changes. Here, the value of the change in resistance represents a function of the concentration of the combustible gas. The sensor can be used for the detection of flammable gases such as hydrogen, carbon monoxide, methane, etc.
Advantages:
- Small size.
- Simple structure.
- Good stability.
Disadvantages:
- No selectivity in the range of flammable gases.
- Need to work with dark fire; the risk of ignition explosion is greater.
Optical Gas Sensors
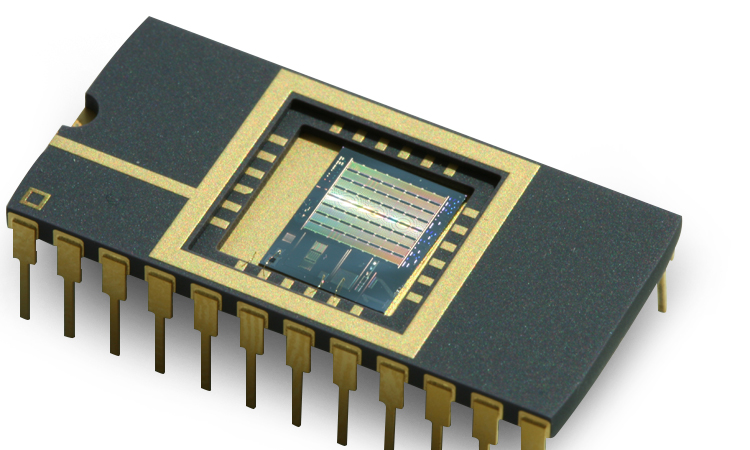
Optical gas sensors are an effective alternative method of measuring flammable gases. Most people will use this sensor for industrial use. Many electromagnetic waves can be used in optical gas sensors. These include infrared gas sensors, ultraviolet gas sensors, and photoelectric colorimetric sensors.
Infrared gas sensors are the typical type of absorbing optical gas sensor. It is suitable for measuring oxygen-free ambient gases or high carbon dioxide concentrations. This type of sensor is based on the infrared absorption spectral properties of the gas to be measured. It is also applicable to the thermal effect operating principle. This operating principle allows one to measure the concentration of a specific gas. Infrared sensors are typically used in the spectral range of 1-25 microns. The types that people commonly use are DIR dispersive infrared and NDIR non-dispersive infrared.
Infrared sensors are very effective at distinguishing between types of gases. NDIR non-dispersive infrared sensors use a spectral light source. It does not have a spectral grating or prism to split the light. Suppose the light passes through the optical path of the target gas into the infrared sensor. We can determine the concentration of the target gas by measuring the intensity of the infrared light entering the sensor. Suppose there is no target gas in the environment. Then its light will not change. Simply put, the target gas enters the gas chamber and absorbs some of the infrared light. Then Infrared light will reduce the intensity of the light reaching the sensor.
Advantages:
- No need to modulate the light source.
- No mechanical moving parts.
- Maintenance-free.
- Long service life.
Disadvantages:
- High production costs.
- Limitations.
Environmental issues have long been one hot topic of concern worldwide. People can use gas sensors to track the concentration of toxic, flammable, explosive, carbon dioxide, and other gases. The emergence of gas sensors helps people to protect the environment better.
Read more: How to Test a Knock Sensor
About GAS Sensor Problem
-
What are gas sensors, and how do they work?
Gas sensors are devices that detect the presence of gases in the air. They use an electronic sensor to measure the concentration of a specific gas in the air and convert it into an electrical signal.
-
What types of gases can gas sensors detect?
Gas sensors detect various gases, including carbon monoxide, methane, hydrogen sulfide, oxygen, and volatile organic compounds (VOCs).
-
What are the applications of gas sensors in different industries?
Gas sensors have a variety of applications in different industries, including industrial manufacturing, oil and gas, environmental monitoring, healthcare, and agriculture.
-
What are the benefits of using gas sensors in industrial processes?
Using gas sensors in industrial processes can help improve workplace safety, reduce the risk of explosions or fires, improve product quality, and increase efficiency.
-
What factors should be considered when selecting a gas sensor?
When selecting a gas sensor, factors such as the type of gas to be detected, the concentration range, the operating environment, and the required response time should be considered.
-
How accurate are gas sensors, and what are the potential limitations?
The accuracy of gas sensors can vary depending on the type of gas sensor and the conditions in which it is used. Some potential limitations of gas sensors include interference from other gases or environmental factors and the need for regular calibration and maintenance.
-
How can gas sensors help improve workplace safety?
Gas sensors can help improve workplace safety by detecting the presence of hazardous gases in the air and alerting workers to potential dangers. This can help prevent accidents and injuries in the workplace.
-
What are the compliance requirements for using gas sensors in industrial settings?
The compliance requirements for using gas sensors in industrial settings vary depending on the industry and the specific application. Businesses should generally ensure that their gas sensors comply with relevant safety and environmental regulations.
-
How can gas sensors be maintained and calibrated for optimal performance?
Gas sensors should be regularly calibrated and maintained to ensure optimal performance. This may include cleaning the sensor, replacing parts as needed, and conducting regular calibration checks.
-
What advancements are being made in gas sensor technology, and what impact will they have on the industry?
Advancements in gas sensor technology are focused on improving accuracy, reducing response time, and expanding the range of gases that can be detected. These advancements are expected to significantly impact the industry, improving workplace safety and efficiency and enabling new applications in areas such as environmental monitoring and healthcare.