Metalworking is a crucial part of manufacturing. During the process, different types of chips in metal cutting are generated, which can affect the quality of the final product. Understanding the properties and types of chips can help optimize the metalworking process. Research has shown that factors such as cutting parameters, tool geometry, and material properties all contribute to the formation of chips. Proper chip management and disposal are also important considerations for workplace safety and environmental impact.
Types of Chips
There are several types of chips that can be generated during the metalworking process. These include continuous, segmented, discontinuous, and powdery chips. The type of chip generated is determined by the material properties, cutting parameters, and tool geometry. Understanding the different types of chips is important for achieving optimal manufacturing efficiency and product quality. In the following sections, we will explore each type of chip in more detail.
Continuous Chips
Continuous chips are long, narrow, and typically curl spirally. They are formed when a high cutting speed, low depth of cut, and low feed rate are used. The shape and size of the chip can vary depending on the tool geometry, cutting speed, and feed rate.
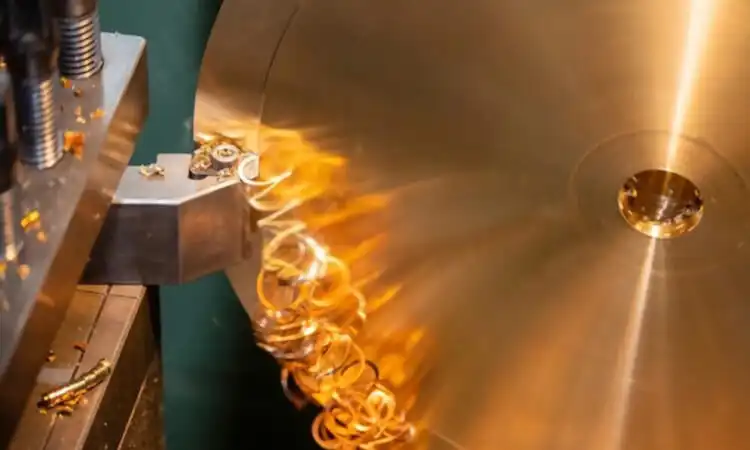
Continuous types of chips are advantageous in many metalworking applications. For example, they help to dissipate heat from the cutting zone, reducing the risk of tool wear and extending tool life. Continuous chips also allow for efficient chip removal. This can help to prevent damage to the workpiece and maintain dimensional accuracy.
However, there are also disadvantages to continuous chips. They can be difficult to manage and dispose of, as they can become entangled around the workpiece or the cutting tool. In addition, continuous chips can cause problems if they become jammed in the machine or interfere with the cutting process.
Related Articles: What Does RFID Labels Consist Of?
Segmented Chips
Segmented chips are a type of chip characterized by a series of segments or discontinuities. They are typically formed when the tool’s cutting edge is irregular or worn or when the material being worked is brittle or hard.
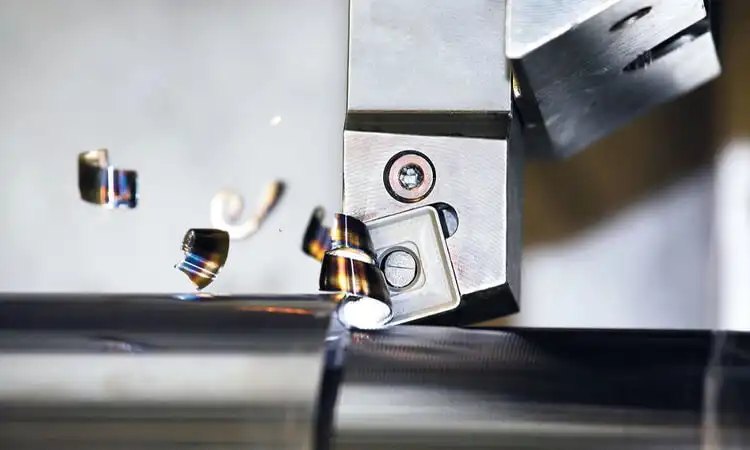
Segmented types of chips can have both advantages and disadvantages in metalworking applications. On the one hand, segmented chips can help to reduce heat generation and prevent damage to the cutting tool. They can also be easier to manage and dispose of than continuous chips. This is because they are less likely to become entangled or cause problems with chip removal.
On the other hand, segmented chips can also cause problems if they are too large or become lodged in the machine. They can also interfere with cutting, leading to lower efficiency and reduced product quality.
Discontinuous Chips
Discontinuous chips, also known as sawdust or particulate chips. It is a type of chip characterized by small, irregular metal particles. They are typically formed when the material being worked is brittle, such as cast iron or some types of steel. The shape and size of the particles can vary depending on the cutting parameters, tool geometry, and material properties.
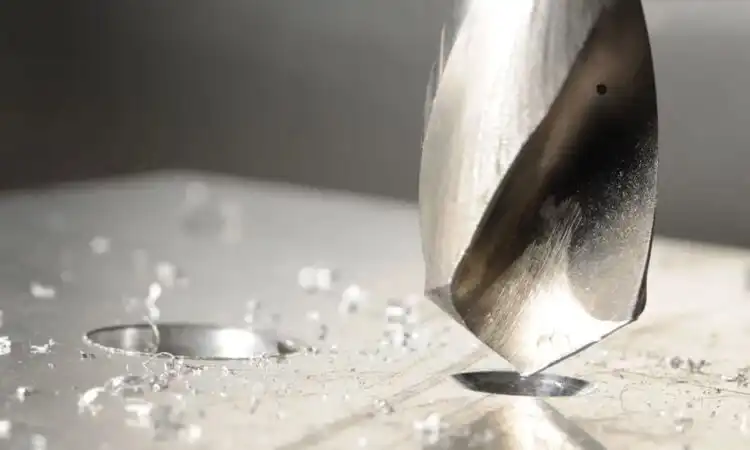
Powdery Chips
Powdery chips are a type of chip characterized by fine, powdery metal particles. They are typically formed when the tool’s cutting edge is blunt or when the material being worked is difficult to machine.
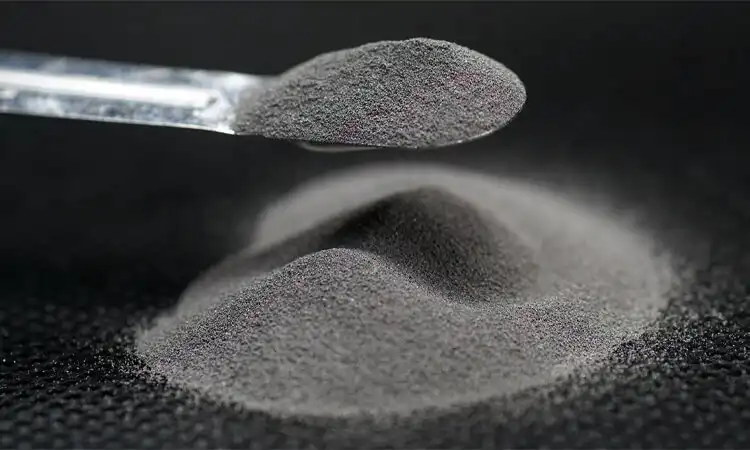
Powdery types of chips can cause problems in metalworking applications. They can be difficult to manage and dispose of, as they can clog filters and other equipment used for chip removal. They can also cause problems with surface finish and dimensional accuracy. This is because they can interfere with the cutting process and leave irregularities on the workpiece surface.
Manufacturers can take several steps to cut the formation of powdery chips. One approach is to use sharp cutting tools that are properly maintained and lubricated. Another approach is to adjust the cutting parameters to ensure the tool is cutting properly and not producing excessive heat. Additionally, choosing the right cutting tool and material can also help to cut the formation of powdery chips.
Continuous Chips vs Segmented Chips vs Discontinuous Chips vs Powdery Chips
Here’s a table that outlines the differences between continuous chips, segmented chips, discontinuous chips, and powdery chips:
Aspect | Continuous Chips | Segmented Chips | Discontinuous Chips | Powdery Chips |
---|---|---|---|---|
Chip Formation | Formed during continuous cutting | Formed during interrupted cutting | Formed in small pieces during cutting | Formed by brittle materials breaking apart |
Chip Size | Long and continuous | Short and segmented | Short and discontinuous | Very small particles |
Chip Shape | Curved or helical | Straight or slightly curved | Irregular or jagged | Irregular or jagged |
Chip Thickness | Uniform thickness | Varies in thickness | Varies in thickness and size | Varies in size |
Cutting Force | Moderate cutting forces | High cutting forces | High cutting forces | Low cutting forces |
Cutting Temperature | Low cutting temperatures | High cutting temperatures | High cutting temperatures | High cutting temperatures |
Material Removal | Efficient material removal | Efficient material removal | Less efficient material removal | Less efficient material removal |
Surface Finish | Good surface finish | Good surface finish | Poor surface finish | Poor surface finish |
Material Properties | Ductile materials | Ductile materials | Brittle materials | Brittle materials |
Applications | Turning, boring, and facing operations | Drilling and tapping operations | Milling and abrasive cutting operations | Grinding and abrasive cutting operations |
Properties of Chips
The size and shape of chips can vary widely depending on these factors. For example, low cutting speeds and high feed rates can result in shorter, thicker chips. High cutting speeds and low feed rates can produce longer, thinner chips. The shape of the chip can also vary depending on the type of tool being used. These include curved or spiral tools producing helical chips and straight tools producing straight chips.
The properties of chips generated during metalworking are important factors that can impact the efficiency and quality of the manufacturing process. The properties of chips are influenced by various factors, such as cutting parameters and tool geometry.
In addition to size and shape, the properties of chips can also affect the manufacturing process. For example, too long or thick chips can become entangled around the workpiece or the cutting tool. They can cause damage or interfere with the process. Chips that are too powdery or fragmented can cause problems with chip removal or disposal.
Factors Affecting Chip Formation
Chip formation is a complex process that is influenced by a variety of factors. Some of the most important factors that affect chip formation include the material properties, the geometry and condition of the cutting tool, and the lubrication.
wikipedia explanation of chip formation:
Chip formation is part of the process of cutting materials by mechanical means, using tools such as saws, lathes and milling cutters.
Material properties can also influence chip formation, such as hardness and flexibility. Materials that are more ductile tend to produce longer, continuous chips. Harder and more brittle materials tend to produce shorter, segmented chips or powdery chips.
The geometry and condition of the cutting tool also play a critical role in chip formation. A sharp, well-maintained cutting tool with the appropriate geometry can help to produce a clean, efficient cut. They can cut the formation of undesirable chip types.
Lubrication is another critical factor that affects chip formation. It reduces heat and friction during the cutting process, enhancing chip formation and prolonging tool life.
Chip Management and Disposal
Effective management and disposal of chips are critical aspects of metalworking processes. Chips can be made of different materials, such as metal, plastic, and wood. Manufacturers must learn proper handling to prevent environmental contamination and ensure worker safety.
Recycling is a popular approach to chip management. It involves collecting and processing chips to recover their raw materials for future use. Recycling can help reduce waste. It also causes energy consumption in manufacturing while also generating revenue through the sale of recovered materials.
Disposal is another approach that requires proper handling and disposal of chips to cut their environmental impact. If disposed of improperly, chips can lead to soil and water contamination. This also has severe health and environmental consequences.
Manufacturers must comply with local and federal regulations to properly manage and dispose of chips. For instance, the Environmental Protection Agency (EPA) sets standards for disposing of hazardous materials. These include metal chips containing oil or other contaminants.
Understanding the characteristics of different types of chips has vast benefits for manufacturers. This knowledge can help them make informed decisions about processing and handling chips in their operations. Proper chip management and handling can help reduce waste. It also helps cut the environmental impact of metalworking processes. In addition, following best practices and regulations can help ensure worker safety. It can also promote sustainable manufacturing practices.
Read More:
21 Top RFID Companies in World
About Types of Chips FAQs
-
What are the Different Types of Chips Generated in Metalworking Processes?
The different types of chips generated in metalworking processes include continuous, segmented, discontinuous, and powdery chips.
-
How do Continuous Chips Differ from Segmented Chips?
Continuous chips are long and continuous, while segmented chips are shorter and have gaps in between.
-
What Factors Affect the Formation of Powdery Chips?
The factors that affect the formation of powdery chips include the material’s ductility, cutting speed, and the rake angle of the tool.
-
How does Tool Geometry Affect Chip Formation?
Tool geometry can affect chip formation by changing the rake. It can clear angles to reduce heat generation, improve chip formation, and prevent tool wear.
-
Can the Lubrication Used in Metalworking Affect Chip Formation?
Yes, the lubrication used in metalworking can affect chip formation. It improves chip formation by reducing heat and friction, extending tool life.
-
What are the Regulations Governing the Disposal of Metalworking Chips?
Regulations governing the disposal of metalworking chips include standards the EPA sets for hazardous materials containing oil or other contaminants.