Modern manufacturing is a vital part of our economy. The United States has a long history of manufacturing, which is why it has thrived as a nation and has been able to compete with other countries. However, there has been a shift from traditional manufacturing methods to more modern ones in recent years. This shift has been driven by the need to reduce costs and increase efficiency. One way that this can be done is through the use of IoT technology.
What is Modern Manufacturing?
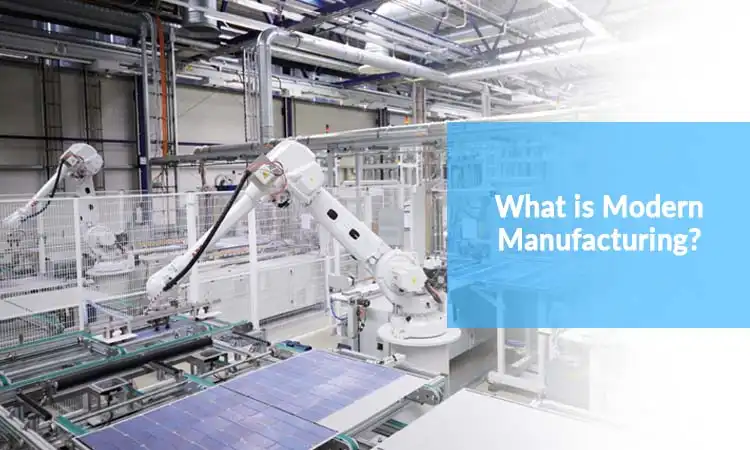
Modern manufacturing is a subset of industrial manufacturing focusing on making products using various technologies. In this modern era, manufacturing companies are shifting from traditional production lines to more automated and advanced practices to meet the demands of their customers.
This shift requires a conscious effort to improve productivity and efficiency. Modern advanced manufacturing uses digital data to help companies better understand their operations and make decisions that improve operations. For example, a modern manufacturing facility can use IoT technology to monitor the supply chain, identify issues before they become costly problems, or even make changes in production to reduce waste.
An example of modern manufacturing is an auto manufacturer like Tesla or Toyota, who have implemented automated assembly lines that produce high-quality cars at low prices with little human intervention required. These processes require advanced robotics and computerized systems that work together with human workers to create vehicles that customers will appreciate and want to buy.
Where did the Modern Era of Manufacturing Primarily Begin?
There is no definitive answer to where the modern manufacturing era primarily began. Modern manufacturing is a complex and multifaceted phenomenon that has evolved over time. It has emerged in different regions worldwide, making pinpointing a single starting point difficult. However, the Industrial Revolution in Britain is widely regarded as a significant turning point in the history of manufacturing. It began a new era of mass production, technological innovation, and economic growth. This period profoundly impacted the world, transforming how goods were produced and distributed and leading to the growth of cities, the emergence of new industries, and the rise of capitalism.
Other regions of the world played important roles in the development of modern manufacturing. The United States, Japan, and Germany emerged as major industrial powers in the late 19th and early 20th centuries. These countries developed their own unique approaches to manufacturing based on factors such as their natural resources, cultural traditions, and government policies.
What is a Key Feature of Modern Manufacturing
A key feature of modern manufacturing is using advanced technologies and automation to improve efficiency, productivity, and quality. This includes using computer-aided design (CAD), computer-aided manufacturing (CAM), robotics, and other digital tools to design, simulate, and optimize production processes.
Another important feature of modern manufacturing is the emphasis on customization, flexibility, and responsiveness to changing market demands. This requires quickly adapting production processes and supply chains to new products, changing customer preferences, and emerging technologies.
In addition, modern manufacturing often involves integrating sustainable and environmentally friendly practices, such as using renewable energy sources, waste reduction, and recycling. This reflects a growing awareness of balancing economic growth with environmental and social responsibility.
Modern Manufacturing Example
When you think about manufacturing, you probably picture large industrial factories. But in recent years, modern manufacturing has expanded to include small businesses and home-based operations.
Here are some examples of modern manufacturing:
- Home appliance manufacturing: The Internet of Things (IoT) revolutionizes how people interact with their homes. The home appliance market is one of the fastest-growing sectors in modern advanced manufacturing, with an estimated $14 billion in sales expected by the future. IoT innovations are increasing efficiency and driving down costs for manufacturers, making it possible for more people to afford appliances and other products at affordable prices.
- 3D printing: 3D printing technology is changing the way that products are created so that they can be customized or made to order. This means that companies can create new products faster than ever before—which means less time waiting on production lines and more time spent innovating!
- Robotic assembly lines: These lines use robotic arms to perform repetitive tasks that require precision, accuracy, and speed. They are designed to replace human workers in line production processes and can cost up to 10 times less than traditional assembly lines.
- Automation: The automotive industry is a prime example of how automation has changed how cars are manufactured. Newer vehicles are more complex than ever and require advanced robotics and computer-aided manufacturing (CAM) to produce them. At the heart of this modernization is the increase in 3D printing. It allows creating custom parts in hours rather than the days or weeks it once took.
- Industry 4.0: It focuses on improved communication between machines and humans by allowing them to interact through wireless networks (Industry 4). This means that when workers need information about the status of their machines or parts, they don’t have to wait for someone else—they can simply access it from their smartphone!
Modern manufacturing is about more than just technology. It’s about the people, their skills, and what they can accomplish together.
Practical use cases for enterprises:
- Boeing has been working on a new process for making composite materials that help them build planes faster and with less waste. The goal is to reduce carbon emissions by 10%.
- The Ford Motor Company is using 3D printing to make custom parts for their cars—and they plan to use it for everything from interior trims to seat covers to even body parts like bumpers and fenders.
- The Toyota Research Institute (TRI) is exploring how robots can be used in production lines to help make cars safer and more fuel efficient. They’ve already tested it with small robots outside of Toyota factories and are looking for partners to scale up production at scale.
Why does a Modern Manufacturing Organization need to Consider IoT?
Modern manufacturing organization is a highly technical field that requires the best of all possible things. It needs to be able to provide the most efficient and effective services while keeping up with current technology. For this to happen, modern advanced manufacturing must consider IoT technology.
IoT technology has been one of the most important innovations for businesses in every industry in recent years. It has become an essential part of modern operations, from large companies like Amazon and Google to small businesses like yours.
It is so important for modern manufacturing organizations because it helps them make better decisions about their processes and improve their efficiency by providing more control over their business operations. This can help your company grow faster than ever before!
Modern manufacturing is a challenging task. It requires high-quality products, low costs, and a strong focus on customer satisfaction. Manufacturers must be able to collaborate with their suppliers, customers, and other parties involved in the manufacturing process to achieve these goals.
IoT can help modern manufacturing organizations achieve these goals by making it easier for them to monitor the status of their production processes and adjust accordingly. By using IoT devices such as sensors and cameras, companies can capture information about their processes at any time, regardless of whether they are operating in production mode. This allows them to respond when issues arise, or opportunities present themselves so they can take full advantage of them while they’re still available.
For example: When a customer contacts a company about an issue with their product, the manufacturer could use IoT technology to determine if there’s anything wrong with the product before sending them another one. Or if a component breaks during shipping—or even after it has arrived at its destination—the manufacturer could immediately identify which part needs replacing and order replacements from their supplier before things go wrong further down the line.
IoT + Manufacturing = Smarter Buildings
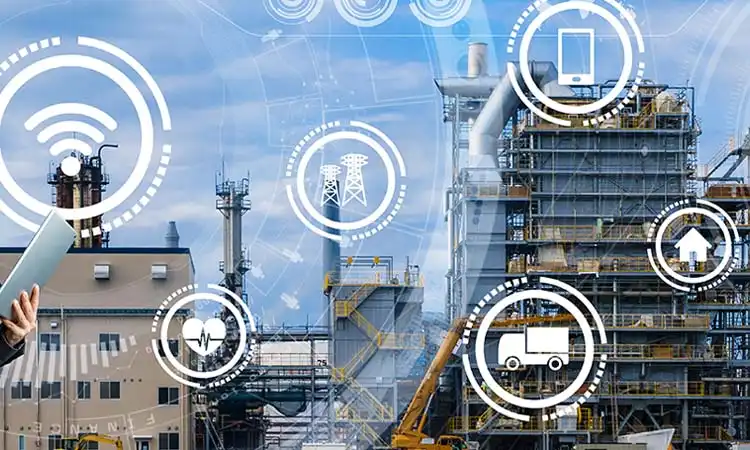
The Industrial Internet of Things (IIoT) allows us to connect our buildings with devices, sensors, and other services used to collect data. This data can be used by the building management system (BMS), which can then use that information to improve efficiency and help operators work more effectively.
This means that modern manufacturing facilities can get smarter about their operations, reducing waste and improving safety. It also means that the facility will be able to collect more data—and use it more efficiently—so there’s less need for human labor or equipment maintenance.
For example, if there’s a leak in one part of the manufacturing process, the BMS can detect it instantly and send alerts to all relevant personnel before things get out of hand. It can tell you if something goes wrong with the production, so there’s no stress on anyone involved.
IoT technology is useful for modern manufacturing organizations because it decreases building and maintenance costs, making buildings more efficient. IoT technology can help companies save money on their buildings by reducing the amount of energy used in them.
This means that you will be able to save money on your energy bills as well as on maintenance costs. IoT technology also helps companies save time since they can monitor the condition of their buildings at all times instead of having to wait for someone else to come in and check up on them every once in a while.
Another benefit that IoT technology has for modern advanced manufacturing organizations is its ability to connect different parts of a building so that they can communicate with one another through sensors and software programs installed within each part of the building itself.
If there is a problem with any part of the building, such as a problem with the heating or cooling system, it will be easier for someone outside of that specific location to know. Because they can use those sensors and software programs directly instead of relying entirely on information from those specific locations.
IoT Technology is Useful for Modern Manufacturing Organizations
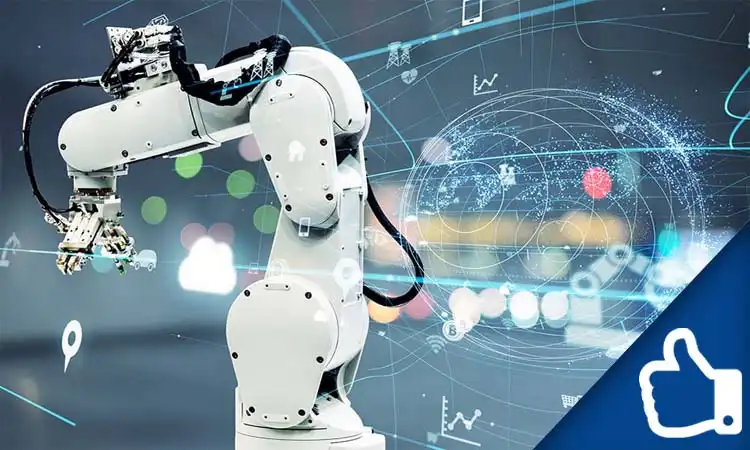
Modern manufacturing organizations have a lot of tools at their disposal to improve efficiency and productivity. One of the most important tools is IoT technology. While it’s not a new concept, IoT technology is gaining popularity as a way to improve quality control and increase efficiency in manufacturing facilities.
The Connected Factory will Improve Productivity
One of the biggest benefits of IoT technology is that it can help manufacturers increase their productivity. With IoT sensors, companies can monitor their operations more efficiently and increase the efficiency of their processes. For example, one company uses an IoT sensor to monitor the temperature in its production line, which allows it to adjust its conveyor belt’s speed accordingly and avoid any issues with overheating or underheating. Another company uses an IoT sensor to monitor the pressure levels in its machines, which allows them to adjust their machines’ settings, so they run more efficiently and produce more products per hour.
Modern Manufacturing Uses IoT Technology to Achieve Increased Efficiency
Modern manufacturing is about efficiency, and IoT technology can help you achieve that. Here are just a few examples of how modern advanced manufacturing uses IoT technology to achieve increased efficiency:
- Supply chain management: With IoT technology, manufacturers can monitor the stock levels of products and when they will be shipped. This means they can plan ahead and ensure enough product is on hand when needed.
- Shrink-wrapping: When you shrink-wrap a product, it reduces its volume by up to 80%. If you were using traditional methods for shrink wrapping, you would need anywhere from 1 to 3 times as much packaging material, with each piece of material being wasted. However, by using IoT technology, companies can shrink-wrap their products without wasting more materials or time.
- Real-Time Monitoring: By monitoring temperature, pressure levels, and other factors in real-time, manufacturers can reduce waste by avoiding unnecessary replacements or repairs on equipment such as pumps or boilers. This also reduces downtime while keeping an eye on maintenance needs before they become urgent issues requiring immediate attention (and increased costs).
Reduced Waste
Companies that use IoT technology can reduce waste by tracking how much raw material is used per product and then adjusting production accordingly so that there is less waste during each production cycle. This means less raw material needs to be purchased or recycled; it also means fewer workers are needed to remove excess materials from storage areas where they might otherwise sit unused until disposed of later down the line when
Using IoT Technology to Improve Product Quality
IoT technology also helps improve quality control by providing real-time feedback on manufacturing processes and events so businesses can fix problems before they become major customer issues (or worse—accidents). For example, a company uses an IoT sensor to monitor how well its products are being produced. Suppose one of these products shows signs of being defective. In that case, it will be identified immediately and fixed before any problems arise with customers’ orders or supply chains at large-scale manufacturing plants worldwide.
IoT Technology Help Bring Transparency to the Manufacturing Process
Manufacturing companies have access to data at a scale never before seen by large numbers of people—and that information can be used to make better decisions about how products are made. For example, if there’s an issue with a particular part of a product. It could be identified instead of waiting until after it’s been manufactured and shipped to customers. This could save millions of dollars in costs and headaches down the line.
Allaying the Fear of a Looming Data Nightmare
One of the most common reasons companies hesitate to invest in IoT technology is that they are afraid of the potential for data overload. As customers increasingly expect product information and service delivery, manufacturers must plan to manage their data security and privacy.
However, this fear is unfounded. Using IoT technology such as sensors, machine learning algorithms, and cloud computing, companies can safely collect, analyze, and store large amounts of data without compromising their customers’ privacy or security.
For example, food manufacturers could capture data about how long their products spoil after being stored in different warehouses and refrigerators over time. And then use that information to improve the packaging or design of future products—they could save money by decreasing waste and reducing costs associated with spoiled food. In addition to improving customer satisfaction through faster deliveries from better-stored foods, this innovation would save businesses money because less food would go bad before reaching consumers.
Using IoT Technology to Reduce the Costs
If you’re buying something from your local hardware store, chances are it will be cheaper than buying online. But what if you could save money by buying online and having it delivered right to your door? That’s what happens with IoT products—their manufacturer often discounts them because they don’t have to pay for shipping and handling costs! With IoT devices, you can buy them cheaper than ever before—and then just look forward to a nice surprise when your package arrives in the mail! You may even find free shipping on your new device if purchased online through an authorized dealer.
Changing Customer Expectations
Customers are now expecting more from their manufacturing facilities than ever before. The Internet of Things (IoT) is a great way to meet these expectations by improving the customer experience, employee engagement, and business operations.
For example, you could use IoT technology to gather data about your customer’s buying habits and preferences so that you can develop new products faster and offer personalized recommendations. Or you could use it to track the quality of your products as they’re being made, eliminating the need for costly recalls.
Improved Employee Engagement
IoT technology can also improve employee engagement by helping you track performance and solve problems faster. For example, if an employee encounters a problem with machinery or other equipment while working, IoT technology could allow them to share their concerns with their manager in real-time. Instead of waiting until after work, they are most likely also tired or distraught and unable to fully think about what needs to be done next – or even if they are still working on something else entirely!
What is the Best Way to Integrate IoT Technology into Your Manufacturing Facility?
The best way to implement IoT technology into your manufacturing facility depends on many factors, including company size, the technology available, and budget. Suppose you have the budget and the right technology in place. In that case, investing in an IoT solution can help you improve employee engagement, customer experience, and overall efficiency is a great idea.
If you’re just beginning to explore the benefits of smart manufacturing solutions for your production line, here are some things you should consider:
- How much do you already know about IoT?
- You might want to start with some resources.
- What kind of data do you already have available?
- You’ll need this information before even considering investing in any new technology, so make sure you have access!
- Are there any regulations that apply to your industry?
- For example, do you need approval from government agencies for communication between devices (like Bluetooth) or sharing personal data (like through social media)? Know what regulations might apply so you can plan when setting up your network.
Implementing IoT Technology is a Long-term Investment
Implementing IoT technology is a long-term investment. It takes time to implement, and it’s not something that can be done overnight. The benefits of implementing IoT technology are numerous, but they aren’t immediate.
The time it takes to implement IoT technology is worth the effort. Implementing IoT technology in an industry can take anywhere from six months to a year before you see any real results. However, once you do begin seeing results, there are many ways that this technology can help your company thrive.
Modern manufacturing is changing, and it’s not just because of the rise of automation and artificial intelligence. This is also because of the digitization of processes, which means various new technologies are coming into play. Modern manufacturing organizations need to consider IoT technology, which will help them improve efficiency, productivity, and quality while cutting waste and improving transparency in their processes.
General Q&A About Modern Manufacturing
-
What is the disadvantage of modern manufacturing?
One disadvantage of modern manufacturing is that it can lead to job displacement and income inequality, as automation and advanced technologies replace human workers in certain tasks. This can negatively impact local communities and workers struggling to find new employment opportunities.
-
Who is the greatest contributor to modern manufacturing practices?
There is no single greatest contributor to modern manufacturing practices, resulting from a long history of technological, economic, and social developments. However, some key figures and innovators in the field include Henry Ford, Taiichi Ohno, and W. Edwards Deming, who made significant contributions to the development of mass production, Lean Manufacturing, and quality management, respectively.
-
Why is modern manufacturing important?
Modern manufacturing is important because it drives economic growth, job creation, and technological innovation. It allows for the mass production of goods and services, making them more affordable and accessible to consumers. It also enables countries to compete in the global marketplace and to develop new technologies and solutions to address societal challenges.
-
How has modern manufacturing evolved since WWII?
Since World War II, modern manufacturing has undergone significant changes and advancements driven by the development of new technologies and the globalization of markets. This has led to a shift towards automation, digitalization, customization, and the integration of sustainable and environmentally friendly practices.
-
What was the first modern industry?
The first modern industry is widely considered to be the textile industry, which emerged in Britain during the Industrial Revolution in the late 18th century. The textile industry was one of the first industries to adopt mechanization and mass production techniques, leading to significant increases in productivity and efficiency.
-
Where was the first modern factory in America?
The first modern factory in America is often credited to the Slater Mill in Pawtucket, Rhode Island, which began operating in 1790. The mill was based on the design of textile mills in Britain and was one of the first factories to use water-powered machinery for spinning and weaving.
-
What is the difference between a factory and an industry?
A factory is a physical location where goods are produced or manufactured. At the same time, industry refers to a group of businesses or organizations involved in producing, distributing, or selling a particular product or service. In other words, a factory is part of an industry encompassing all the businesses and activities related to a particular sector or market.