Inertial sensors are essential components of many modern devices. They are used to measure acceleration, orientation, and angular velocity. These sensors are particularly useful in applications that require precise positioning or movement tracking, such as aerospace, robotics, and autonomous vehicles. With technological advancements, inertial sensors have become smaller, more accurate, and more affordable. This blog post will overview inertial sensors, their assembly, applications, and future trends.
What are Inertial Sensors?
An inertial sensor detects and measures an object’s acceleration, tilt, and vibration. It converts inertial forces into measurable electrical signals. It is an interesting and useful ability. It is important for solving navigation, orientation, and motion carrier control. Inertial sensor components typically include accelerometers and angular velocity sensors (gyros). Their single, dual, and tri-axis combinations IMU and AHRS play an important role.
Microfabrication technology to produce MEMS inertial sensors becomes possible. This technology is used to produce using single crystal silicon sensor elements. These produced micron-level sensors can meet almost all major system design drivers. MEMS inertial sensors have the same principles as macroscopic inertial sensors. It can detect the slightest change in an object several meters long using small sensor cells. These slightest changes include the object’s position, orientation, and acceleration.
There are two main types of MEMS inertial sensors. One is an accelerometer that can measure linear acceleration in one or more axes. People often use this accelerometer. The other is a gyroscope that can measure angular motion. These sensors all seem to be made by people for specific applications. It is because these inertial sensors meet the needs of many different applications.
These sensors’ bandwidth, resolution, and dynamic range vary depending on the product. For example, an automotive airbag release system is very high on the inertial sensor. It must have a bandwidth of up to 0.5KHz and a resolution of over 500mG. Its dynamic range must be approximately within +/-100G. Other types of equipment have different requirements for these ranges. Air microgravity measurement instruments need an inertial sensor with broadband of 0-10Hz. But its resolution must be accurate to <1µG and a dynamic range of less than +/-1G.
Here’s a PDF on inertial sensor technology for navigation applications.
Inertial sensors occupy an extremely important position in any application or equipment. It is part of the larger control system of the device or application. If you only know an object’s acceleration or angular motion, the information is not very useful. It is because the information collected from this sensor is usually used to control the device’s motion. Of course, it may also activate an actuator, such as opening an airbag in a car.
Inertial Sensor assembly
Accelerometer Sensors
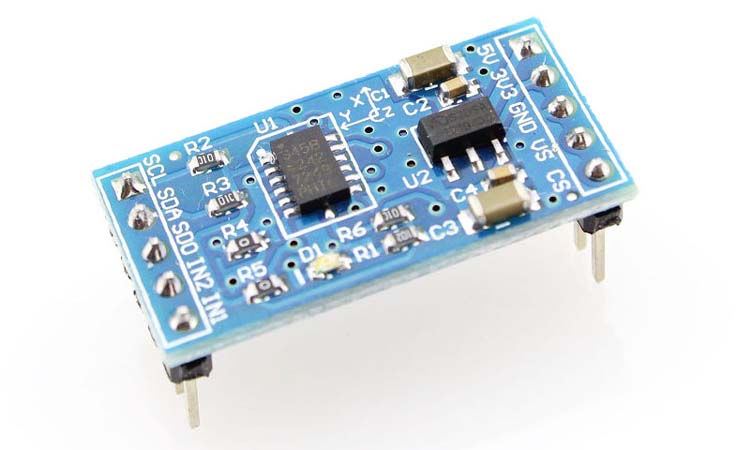
The accelerometer sensor is an important component of an inertial sensor, also called an accelerometer. The sensor supports the measurement of acceleration in one or more axes. The accelerometer consists of a mechanical sensor element (standard mass block) and a detection circuit. On the other hand, the sensing element consists mainly of a mass block connected to a reference frame by a mechanical suspension system. The detection mass is a very small seismic mass in a MEMS sensor. On the other hand, the mechanical suspension system is made of high-quality silicon springs.
The sensor is subjected to inertial forces due to acceleration. Now, the detection mass deviates from its stable position. Newton’s second law of motion explains it well. The Laplace equation can express the deflection of a mass block against acceleration.
X / a = 1 / (s 2 + b / m + s × k / m)
In this equation, different letters stand for different things. x stands for the displacement of the mass block, and a is the acceleration. s denotes the Laplace operator, and b is the damping factor. m means the mass of the mass block. k is the mechanical spring constant of the suspension system.
The resonant frequency of the sensor can be expressed as:
f n = √ ̄(k / m)
The quality factor equation is expressed as:
Q = √ ̄ (m × k) / b
The sensitivity of the sensor (in the open loop) is expressed as:
S = m / k
From the above algorithm, it is obvious that a rule can be seen. By increasing or decreasing the sensitivity, the resonant frequency of the item changes. With a closed-loop system, people can freely adjust this trade-off. The damping factor determines the largest bandwidth of the accelerometer. The damping factor is typically variable in MEMS accelerometers. This coefficient increases with the displacement of the detected mass.
The displacement of the mass block is measurable in all micromechanical accelerometers. People can measure this displacement distance through a position measurement interface. The measurement method is the same as in the capacitance measurement. A movable plate attached to the mass block moves between fixed capacitive electrodes. Several different types of sensing mechanisms are applied in the accelerometer design. These sensing methods include piezoresistive, piezoelectric, capacitive, optical, and tunneling current.
Accelerometers support open-loop or closed-loop systems. The open-loop accelerometer will use an electrical signal from the position measurement interface. And then, the accelerometer will convert the electrical signal to an output signal. Because open-loop accelerometers are easy to build, most people choose to use them. Open-loop accelerometers also have a disadvantage – people must manage them with high tolerances. The damping factor is because the accelerometer has a variable spring constant. The mass displacement of an open-loop accelerometer also requires a non-linearity check.
A closed-loop accelerometer allows the detected mass to return to its resting position. It relies on a feedback system that wants to track the feedback force exerted by the mass. This feedback force is proportional to the closed-loop accelerometer acceleration. The feedback force cancels out with the non-linearities, and the sensitivity depends on the feedback control. The feedback signal can also be used to control the dynamics of the sensor using an electrical signal controller. It can be driven by electrostatic, thermal, or magnetic forces to return the test mass to its resting position. People can often display the feedback signal in analog or digital form. All these designs add to the complexity of the sensor.
There are many types of accelerometers, and the following are some common methods of acceleration sensing:
- Mechanical accelerometers
- Optical and surface acoustic wave accelerometers
- Fluid-based accelerometers
- Viscous float-based accelerometers
- Pressure-driven accelerometers
- Unprocessed fluid-based accelerometers
Angular Velocity Sensor

An angular velocity sensor also called a gyroscope, is designed to measure the rotation of an object. MEMS gyroscopes mainly use the Coriolis principle. Two forces impede a mass moving in a rotating system. These two forces are the force perpendicular to the axis of rotation and the force in the direction of motion. A mechanical mechanism usually constructs a MEMS gyroscope. This mechanical structure is driven into resonance by the Coriolis force. It excites secondary oscillations in the same or secondary structure. Of course, the Coriolis force is smaller than the driving force. Thus, all MEMS gyroscopes use the Coriolis force phenomenon in their vibrating structure.
A pair of springs connected to a mass block in the inner frame form the vibrating structure. The inner and outer frames are connected by another set of orthogonal springs. A capacitance-sensitive finger exists between the inner and outer frames. This capacitance-sensing finger is also connected along the orthogonal springs. The Coriolis force increases with the angular velocity of the rotating object as the velocity of the object increases. It also follows towards or away from the axis of rotation. The inspection mass is then driven continuously sinusoidally through the internal spring. The resonant test mass will be subjected to the Coriolis force as the system undergoes rotation. The mass will be subjected to this force by an orthogonal spring between the inner and outer frame. This force will make it change. This force will change the distance between the capacitive sensing fingers. Thus, the angular velocity sensor outputs the relevant electrical signal simultaneously. This signal is proportional to the Coriolis force.
The accuracy range of different angular velocity sensor subsets will deviate. Common types of angular velocity sensors are:
- Dynamically Tuned Gyroscope (DTG)
- Vibration Gyroscopes
- Optical Gyroscopes
- Fluid-based Angular Velocity Sensors
- Rate Integration Gyroscopes
- Magnetohydrodynamic Gyroscopes
- Dual-axis Rate Sensors
- Jet and Vortex Gyroscopes
- Micromachined Fluid-Based Angular Velocity Sensors
Inertial Sensor Applications
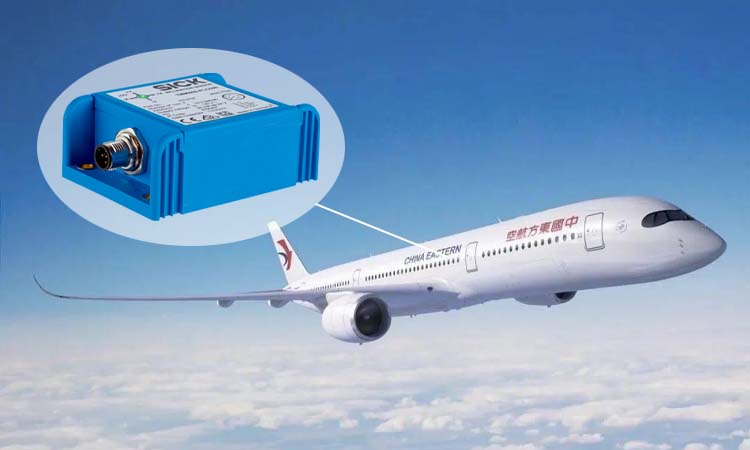
Inertial sensors can be used in many different industries. Before, inertial sensors were usually limited to military and aerospace applications. The rapid development of MEMS inertial sensors is becoming available for more applications. It is highly sought after in the automotive and various consumer electronics fields.
People use accelerometers for automotive airbags and seat belts in the automotive industry. And gyroscopes are used in applications such as anti-rollover protection and automatic indicators.
The field of consumer electronics has a broader range of applications. People can use it in cameras, virtual reality headsets, smart toys, and gaming keyboards. Smartphones and tablets used in our lives are equipped with inertial sensor systems. It is mainly used to detect screen rotation and games and enhance the user’s sense of reality experience.
It also supports users to use it to check the position and orientation of robot manipulators and driverless robotic vehicles. These sensors can also be used in the medical field. It can help doctors track patients suffering from specific diseases. For example, monitoring patients who have Parkinson’s disease. High-precision inertial sensors are mostly used in military and aerospace applications. People can use it in smart munitions, collision detection, and plane/missile flight control.
Related Reading: The use of inertial sensors system for human motion analysis
Future Trends in Inertial Sensors
The accuracy of inertial sensors has improved significantly over time. It has greatly met the needs of navigation and guidance applications’ size, cost, and accuracy. Over the past few years, it has evolved from being purely mechanical to being able to incorporate a variety of technologies. These technologies include nuclear magnetic resonance technology and cold atom technology. It can also use many physical phenomena to accurately calculate the power applied to the object. But, the error nature of inertial sensors is still a challenge that needs to be studied. I believe people will soon overcome this challenge.
Acceleration sensors and angular velocity sensors are important components of inertial sensors. However, inertial sensor technology covers various applications in different industries. However, depending on the nature of the product, the choice of inertial sensor components to be formed can vary. Not every inertial sensor is the same.
About Inertial Sensor FAQs
-
What are inertial sensors, and how do they work?
Inertial sensors are devices that measure motion and orientation by detecting changes in acceleration and rotation. They work by using microelectromechanical systems (MEMS) to detect changes in the movement of a small mass.
-
What are the different types of inertial sensors, and how are they used?
The two main types of inertial sensors are accelerometers, which measure changes in acceleration, and gyroscopes, which measure changes in rotation. They are used in various applications, including navigation, motion tracking, and robotics.
-
How are inertial sensors used in navigation and positioning systems?
Inertial sensors can be used with GPS and other positioning systems to provide more accurate and reliable navigation. They can also be used in indoor positioning systems where GPS signals are unavailable.
-
How do inertial sensors improve motion tracking and analysis in sports and fitness applications?
Inertial sensors can provide athletes and fitness enthusiasts with real-time data on their movement and performance, such as speed, acceleration, and jump height. This data can be used to improve training and prevent injuries.
-
How are inertial sensors used in robotics and automation?
Inertial sensors can be used in robotics and automation to provide feedback on the movement and orientation of robots and other machines. This can improve precision and accuracy in manufacturing and other industries.
-
What are the potential applications of inertial sensors in healthcare and medical devices?
Inertial sensors can be used in healthcare and medical devices to monitor and track patient movement and activity, such as in rehabilitation or physical therapy. They can also be used to detect and prevent falls in elderly populations.
-
How can inertial sensors detect and prevent falls in elderly populations?
Inertial sensors can be used in wearable devices to detect changes in acceleration and orientation that may indicate a fall. This information can alert caregivers or emergency services and help prevent injuries.
-
What are the ethical implications of using inertial sensors in surveillance and security systems?
Using inertial sensors in surveillance and security systems raises ethical concerns around privacy, data security, and potential misuse. It is important to balance the benefits of improved safety and security with the potential risks to individual rights and freedoms.