Inventory management is crucial for any business to succeed. Properly managing inventory helps reduce costs and increase efficiency. However, according to a survey, 43% of small businesses don’t track their inventory, and 17% don’t even know what inventory management is. This article will outline the best practices for effective inventory management based on research and industry knowledge.
Inventory Management Basics information
Inventory management refers to the process of managing and organizing a company’s inventory. It ensures the right inventory quantity is available at the right time and cost. This includes tracking inventory from the purchase order stage to the sale of goods in the supply chain. Effective inventory management includes various aspects such as order management, and finished products.
Implementing inventory management best practices helps meet customer needs and increase their satisfaction. One of the best practices is having accurate demand forecasting to maintain optimal stock levels and avoid stock shortages. Poor inventory management can accumulate dead or unsold stock levels, negatively impacting a company’s cash flow.
There are five key stages of inventory management: purchasing, production, stock holding, sales, and reporting. Purchasing involves acquiring raw materials or buying products for resale. Production involves preparing the final product from its constituent parts. Stock holding refers to storing raw materials and final products before sale. Sales involve making products available to customers and collecting payment. Reporting generates reports on cash flow and profitability. Companies can use this report to plan their next operations.
11 Inventory Management Best Practices
ABC Analysis Classification
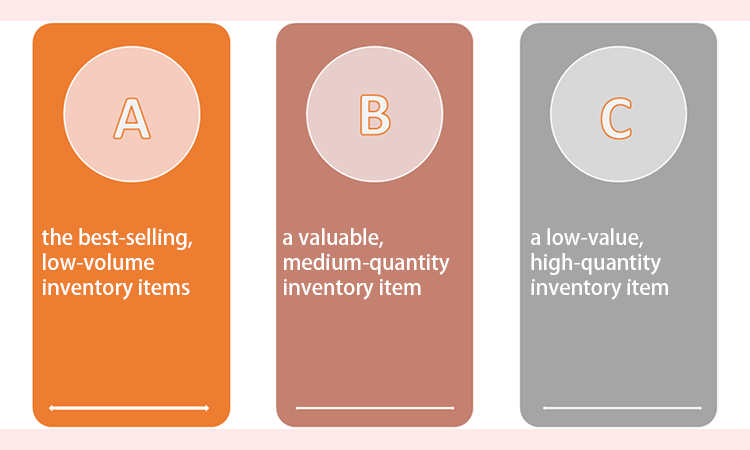
Keeping your inventory in order can help improve employee productivity. ABC analysis is a simple and effective technique. It will arrange your inventory into a hierarchy of items from the most important to the least important.
The following are ABC analyses in inventory management practices:
- Category A is the best-selling, low-volume inventory items
- Category B is a valuable, medium-quantity inventory item
- Category C is a low-value, high-quantity inventory item
Generally, Class A requires periodic ordering and long-term quality reviews. It needs to ensure product quality and enough stock. Category B usually requires monthly ordering. Category C is for inventory items purchased in large quantities with low demand for later ordering. Sorting inventory items based on ABC analysis helps optimize your inventory storage space. It also simplifies order fulfillment.
Quality Control
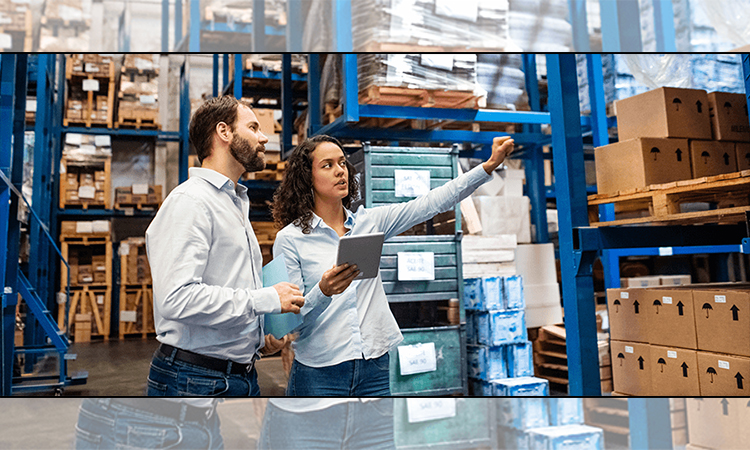
Quality control is needed for any size business. Control of inventory quality throughout the process can increase customer satisfaction. It can also significantly increase the growth rate of your business. For a successful enterprise, the quality of its products is mostly guaranteed.
It is usually easy to start a quality control program. You can create a checklist. Then ask your employees to strictly follow all the procedures on the list when checking the received goods. Although there is more work for the workers, the quality of your products is guaranteed. Customers will have confidence in the quality of your products, and repeat business will increase.
You can usually ask your employees to do these checks:
- Whether the product is damaged (leaks, tears, or broken seals)
- Whether the product description matches the buy order (product color, style, size)
- Sales Price and Terms
Make sure employees are all operating in the same manner when receiving inventory. All inventory boxes are verified, received and unpacked, and accurately counted. Then the quality of warehouse products will naturally improve. They will also know to take out and return to the supplier any products found during inventory count that do not meet company standards. This inventory management best practices effectively prevents unnecessary increases in inventory levels. Employees also don’t have to worry about providing customers with unsuitable goods. Of course, companies don’t just have to make sure their products meet quality requirements. It would be best if you also controlled the warehouse environment in which it is stored tightly. Unsuitable environments can damage products, such as light, temperature, and humidity.
Optimize the Picking and Packing Process
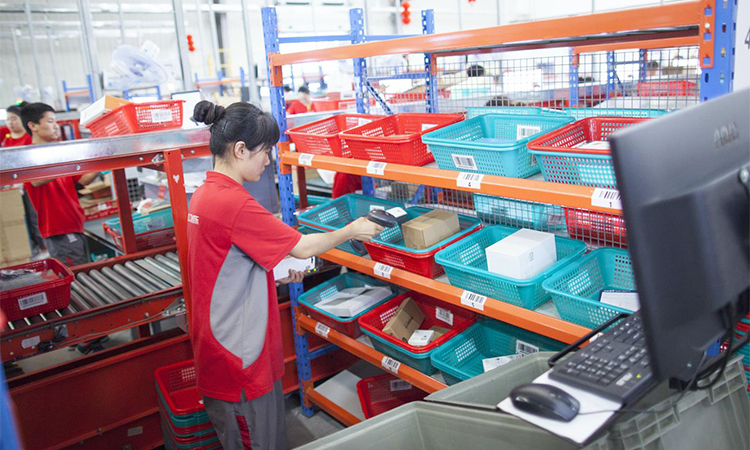
Procedures and tools that employees can use during the picking and packing process. These programs and tools help them fulfill customer orders quickly and efficiently.
You can achieve more efficient inventory management by optimizing the picking and packing process by:
- The best-selling items are placed closest to the packing station
- Clean the environment in each area and get rid of unwanted debris
- Implement and program inventory management software for the warehouse
- Carefully check and accurately count each order
- Use bar codes or RFID labels on in-stock items
These hands-on approaches to optimizing the pick and pack process benefit your business. Bestsellers close to the packing station save employees time looking for items. It also increases their productivity. A clean working environment allows employees to work more comfortably. Inventory management software can help pickers find the items they need faster. Using barcodes or RFID tags in the warehouse makes it easier for employees to count merchandise.
Related Articles:
- RFID Labels Structure Analysis
- Best Tools Management Software in 2023
- Why Should You Use Warehouse Barcodes?
Establishing Inventory KPIs
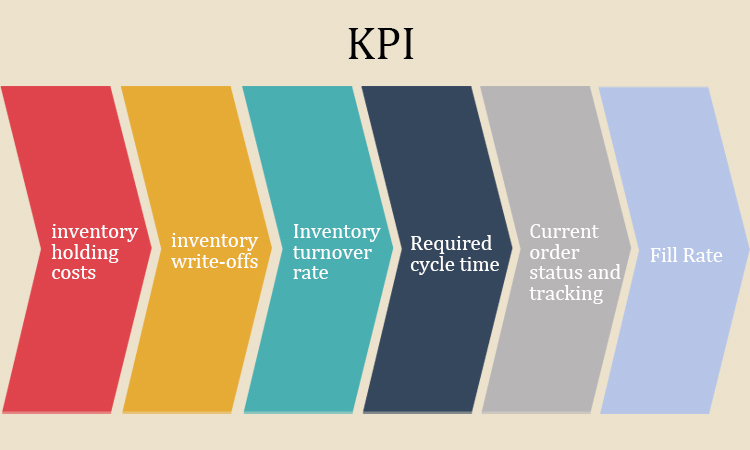
Inventory KPI is critical to the strategic decisions of a business. It measures how well a specific target of the business performs in a specific area at a specific time. It will be presented to the business with clear weekly/quarterly/yearly milestones. It can effectively eliminate the anxiety of managers. The data provided by the inventory KPI will assist you in making the most informed business strategies.
For the Inventory KPI, there are 6 points you need to focus on:
- Current inventory holding costs
- Current inventory write-offs and inventory write-downs
- Inventory turnover rate
- Required cycle time
- Current order status and tracking
- Fill Rate
Combining these six inventory KPIs yields data that better understand how well your target items are selling.
The Lot and Expiration Tracking
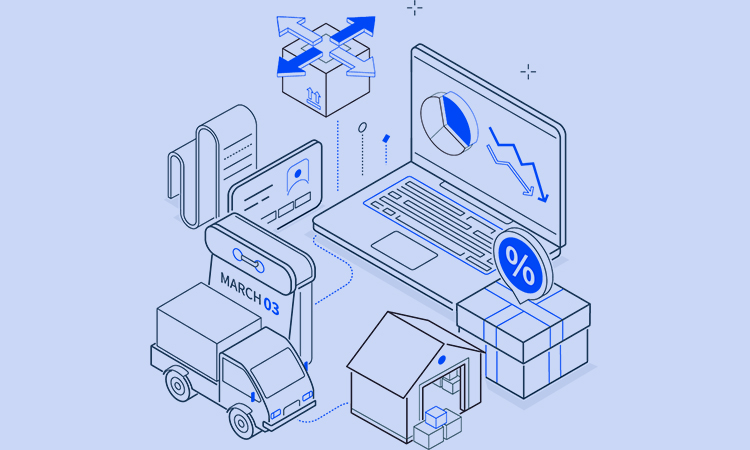
The lot and end tracking process of goods in the distribution chain uses lot numbers and expiration dates. A “lot” is usually a specific group of items produced simultaneously using the same materials. Companies use an automated lot tracking system to enter information about all products in a lot for quick access purposes. It is particularly useful in special situations, such as product recalls. Selecting batches and end dates for tracking is important for companies. It prevents inventory damage and ensures which batches are sold first. It also helps you ensure that you are selling expired consignment items. It also provides accurate data allowing you to delete specific batches in the event of a product recall.
The Exact Reorder Point Formula
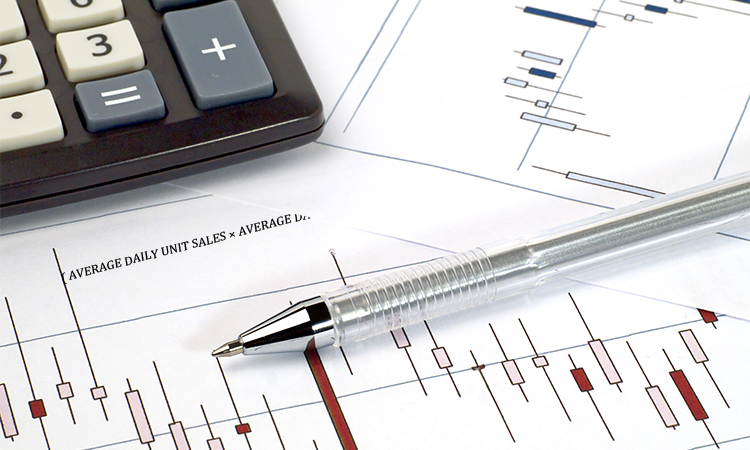
When you should order more inventory is one of the issues that businesses need to worry about for inventory management. The reorder point formula can help you reach the point where you maintain the least inventory before you need more. It will tell you approximately when to order more inventory. The Reorder Point Formula is a proven mathematical equation. Simply put, it is a proven mathematical way to help you order the right amount of stock at the right time. It will keep you from becoming a victim of market spikes or crashes.
In the order point formula:
( AVERAGE DAILY UNIT SALES × AVERAGE DAYS AHEAD ) + SAFETY STOCK = REORDER POINTS
Safety Stock
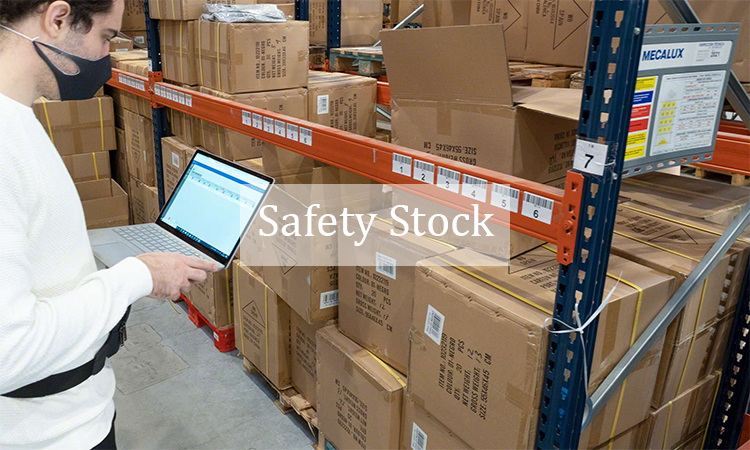
Companies must maintain a small amount of safety stock. These stocks protect against surprises due to temporary changes in market demand and delivery times. Safety stock is the inventory that protects your business in an unforeseen situation. Without safety stock, you could suffer serious losses. These losses include lost revenue, lost customers, and lost market share. Safety stock is one of the keys to inventory management best practices.
By using it, companies can reap many benefits:
- Effectively prevent unexpected demand surges.
- Avoid out-of-stocks
- Compensate for inaccurate market forecasts
- Buffer against over-expected lead times
Safety stock provides an adequate buffer for companies facing unexpected situations. It can also help companies effectively reduce unnecessary customer and property losses. Safety stock plays an extremely important role in the operation of a business.
Optimize Inventory Turnover
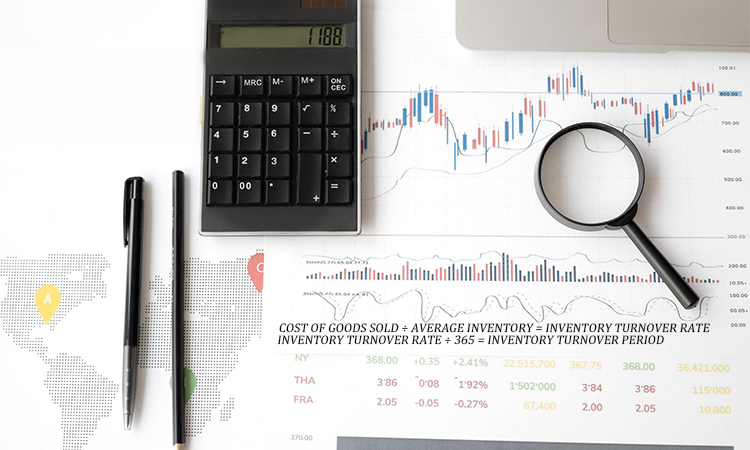
Optimizing your inventory turnover is a best practice for inventory management. It is a measurement. It primarily measures the number of times inventory is sold or used within a specified period. It is usually calculated on an annual basis. Enterprises can better understand their products by calculating their inventory turnover rate. Businesses will have a clear understanding of the market demand for their products. They can also know how much inventory may expire. Companies can also optimize their operational strategies while knowing this. Then think about what next steps the business needs to take to sell or increase its inventory.
A simple formula for calculating inventory turnover:
COST OF GOODS SOLD ÷ AVERAGE INVENTORY = INVENTORY TURNOVER RATE
Determine the time required to turn this inventory:
INVENTORY TURNOVER RATE ÷ 365 = INVENTORY TURNOVER PERIOD
In calculating its inventory turnover rate, the company can do more to improve it. For example, try setting prices and clearing out obsolete inventory. It is also possible to forecast customer demand and allocate inventory to other warehouses.
Related Articles: 7 Warehouse Organization Measures to Improve Efficiency
Automate All as Much as Possible
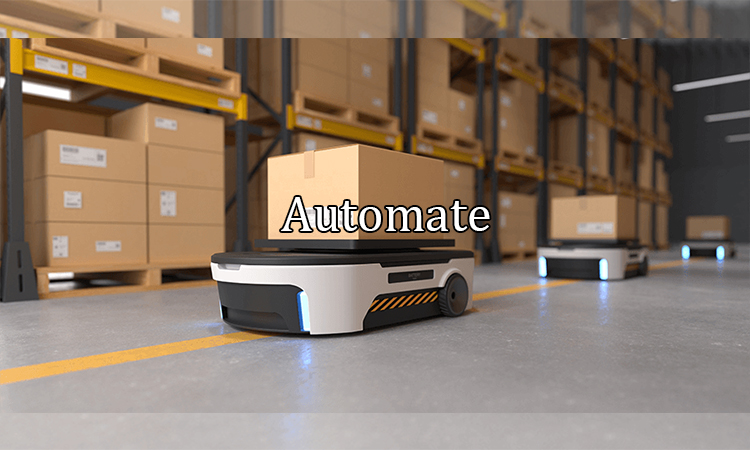
Systematizing some or all of your workflow can help improve efficiency. It also reduces reliance on manual labor. There are many benefits to companies adopting technology to manage a network of work components centrally. It can also reduce the need for manual labor in enterprises, thereby reducing labor costs.
Automating part or all of a company’s supply chain can free up employees while improving productivity and accuracy. A McKinsey report predicted a future trend. Global economic productivity will increase due to automation. Global GDP will increase by 0.8% to 1.4% per year.
Businesses can automate their workflow with the right systems:
- Customize the storefront experience specifically for B2B and B2C buyers
- Set memos for your purchasing and ordering processes
- Batch operations for high-order volume applications
Adding Inventory Packages is the Effective Ways of Inventory Management Best Practices
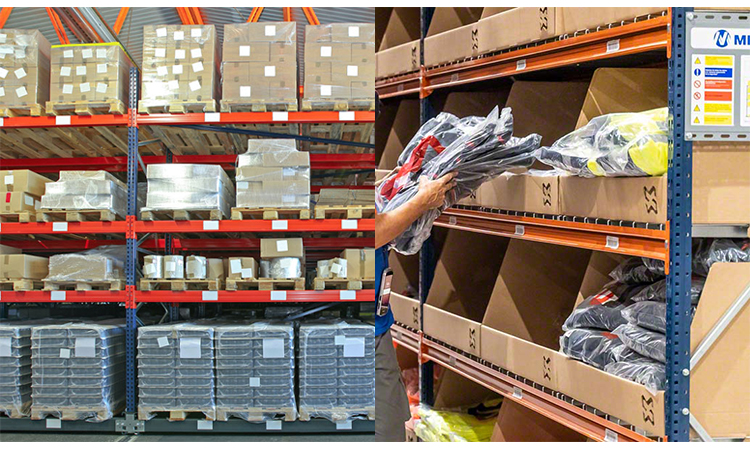
An inventory package is when individual items are combined, packaged, and sold as one unit. You can also call it a product bundle. Usually, whenever sets or bundles of items are sold, the inventory system automatically connects each item to the sale.
Companies can choose to benefit from B2C and B2B through a variety of bundling options. For example, customizing package sizes and creating different bundles of products.
Custom package sizing is primarily for bundles sold with many product combinations. It is equivalent to creating a new product from your bundle. You can also choose different styles of products to make up a bundle, such as pink pajamas and white slippers. People can easily achieve this approach with the bundle package feature.
Increasing inventory packages is extremely beneficial to company operations:
- It can increase the average order value
- Can reduce current holding and shipping costs
- Provides customers with greater convenience and flexibility of merchandise
- It is extremely effective in tracking and maintaining inventory levels
- Can prevent inventory from becoming stagnant
Adopting Cloud-Based Inventory Management Software
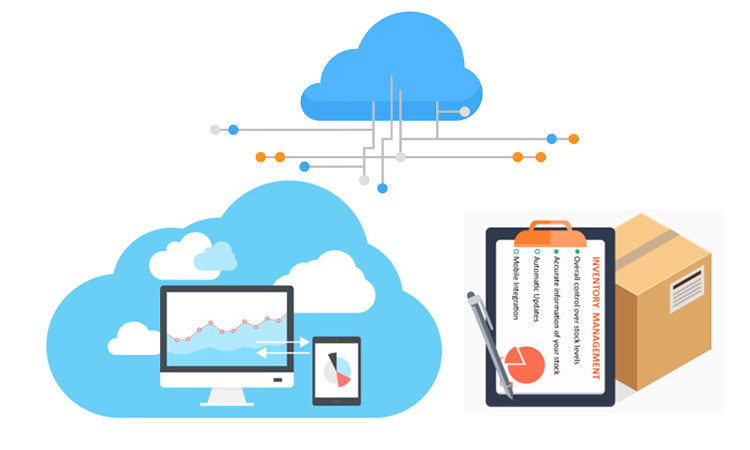
Adopting cloud-based inventory management software is a best practice for enterprise inventory management. We need to stop adopting Excel. Spreadsheets are time-consuming and don’t always reflect accurate inventory levels. Cloud-based inventory management software has more features than a locally installed application. While there is essentially a more fee to use it, its new features allow you to upgrade seamlessly in the future if you need to. You don’t have to worry about what kind of inventory management software you will need in the future when your company grows larger.
Usually, you need to find a “package” that fits your specific functional needs and team size and pay a subscription fee. Suppose your business grows dramatically later, and your current package no longer meets your needs. You can upgrade with just a few clicks. One or more companies back each cloud-based inventory management software. They are there to answer questions and fix problems you face with the software. They are also constantly upgrading the functionality of the original software. Of course, try to avoid picking up bad inventory management software. It is necessary to strictly screen cloud software companies.
Put technology, process, and inventory management best practices into action. They can help companies stand out in a competitive market. However, best practices inventory management will vary depending on the industry and size of the company. But in general, it’s best to get the right “parts” on your terms and at the best cost.
General Q&A About Inventory Management Best Practices
-
What are the benefits of effective inventory management?
Effective inventory management can improve cash flow, better customer service, reduce stockouts and increase profitability.
-
How can I determine the optimal inventory levels for my business?
The optimal inventory levels for your business can be determined by analyzing historical sales data, forecasting future demand, and considering lead times and replenishment frequency.
-
How can I reduce inventory holding costs?
Inventory holding costs can be reduced by optimizing inventory levels, improving accuracy, and reducing lead times.
-
How can I improve inventory forecasting accuracy?
Inventory forecasting accuracy can be improved by using historical sales data, analyzing market trends, and adopting advanced forecasting methods.
-
What are the key performance indicators (KPIs) for measuring inventory management effectiveness?
KPIs for measuring inventory management effectiveness include inventory turnover, stockout rate, order accuracy, and carrying costs.
-
How can I prioritize inventory management tasks to maximize efficiency?
Inventory management tasks can be prioritized by setting clear goals and objectives, analyzing data to identify areas of improvement, and implementing a structured approach to task management.